OTTO-CHEMIE
Client: Hermann Otto GmbH Location: Fridolfing, Bavaria, Germany
From the outside, all that can be seen are two silver metallic silos that lend the sober white building some flair: But inside, production processes run entirely digitally according to the Industry 4.0 standard, thanks to evon XAMControl.
A closed system from delivery to filling of OTTO’s sealants
The Hermann Otto GmbH, or OTTO for short, was founded in 1881 and is a traditional Bavarian company. It has been producing and selling silicon sealants and adhesives based on silicon, polyurethane, silane-terminated polymers (hybrid) and acrylates since the 1960s.
The new factory in Kaltenbrunn produces popular OTTO sealants in large volumes and profits hugely from the high-tech plant based on evon XAMControl. The manufacturing process is conducted almost completely fully automatically and in a closed system. This is in contrast to the previous production methods that continue at the site in the Krankenhaus-straße to manufacture in small batches and with a comparably high level of employee intervention in the individual process steps. The raw materials in Kaltenbrunn, namely the polymer from the tank and the silica from the silo, are automatically dosed and fed into the mixing container. The introduction of additives and colour pigments for each product colour is achieved via a static mixer in the filling section of the cartridges. Just as for the filling, robots print, package the items in cartons and complete the palletization completely automatically.
The centrepiece: Process control system evon XAMControl
The interaction of software, electronics and the machines themselves plays a major role in ensuring that production processes run smoothly and that quality is consistent. Specialists from evon teamed up with those in OTTO to develop a tailored process control system based on evon XAMControl to control and monitor all processes in the fully automated plant. A digital control room that displays the entire production process and its data gives the production manager insights into current processes and enables the exact source of any faults to be located and, if required, permit manual intervention. Data recording enables the processes to not only be monitored, but also analysed and traced. A crucial element for production is the integrated maintenance plans and the notification of faults (SMS, email).
It is not only the production aspect that is integrated in the process control system, evon XAMControl, but also logistics. This offers a series of advantages: On the one hand for the logistics area, since stock level monitoring brings more security in to the production process and the commissioning with tablet and handheld devices guarantees seamless tracing. On the other hand, the complete production of supply media (heating, compressed air, etc.) for the site and the process can also be monitored and controlled using the same software solution.
evon XAMControl communicates in real-time with OTTO’s ERP system. This is responsible for the overall corporate planning and control: From purchasing and stock management, procurement and order fulfilment, up to controlling.
evon XAMControl supports, the human is in charge
The advantages of this closed system are obvious and are also a clear goal of Industry 4.0 since using automation eliminates the typical vinegar smell of the acidic cross-linking raw materials and dust pollution caused by the silica in their dry state. Although the otherwise unavoidable side-effects of the production process are not a health risk, they are unpleasant for the employees. In addition, a large proportion of the heavy lifting work is now supported by machines. From now on, the OTTO team can concentrate on quality assurance. And the team remains indispensable: The pre-produced colour pigments and mixtures need to be prepared and the sealants must be made available to the individual production lines. Colour matching still requires a practiced human eye, despite the use of an optical spectrometer. The employees in quality assurance compare samples from the current batch with the corresponding colour reference template. So despite all the machines, the human remains in charge. All in all, the integration of Industry 4.0 in OTTO’s new factory enables the highest degree of productivity while simultaneously maintaining OTTO’s high and unchanging demands on quality.
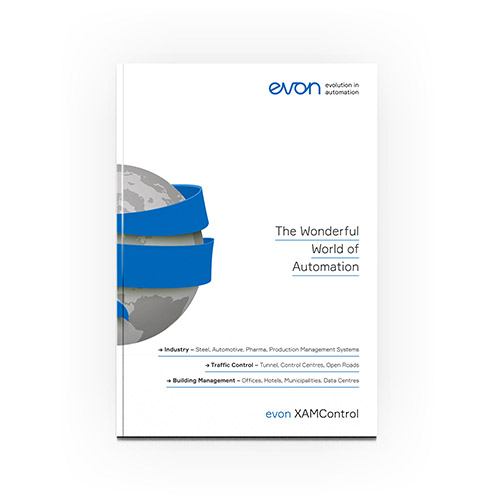
More about evon XAMControl?
evon XAMControl summarized in a PDF, just fill in the form and we will send you the download link immediately.